Cutting Effect of High-Speed Precision Spindle Motors
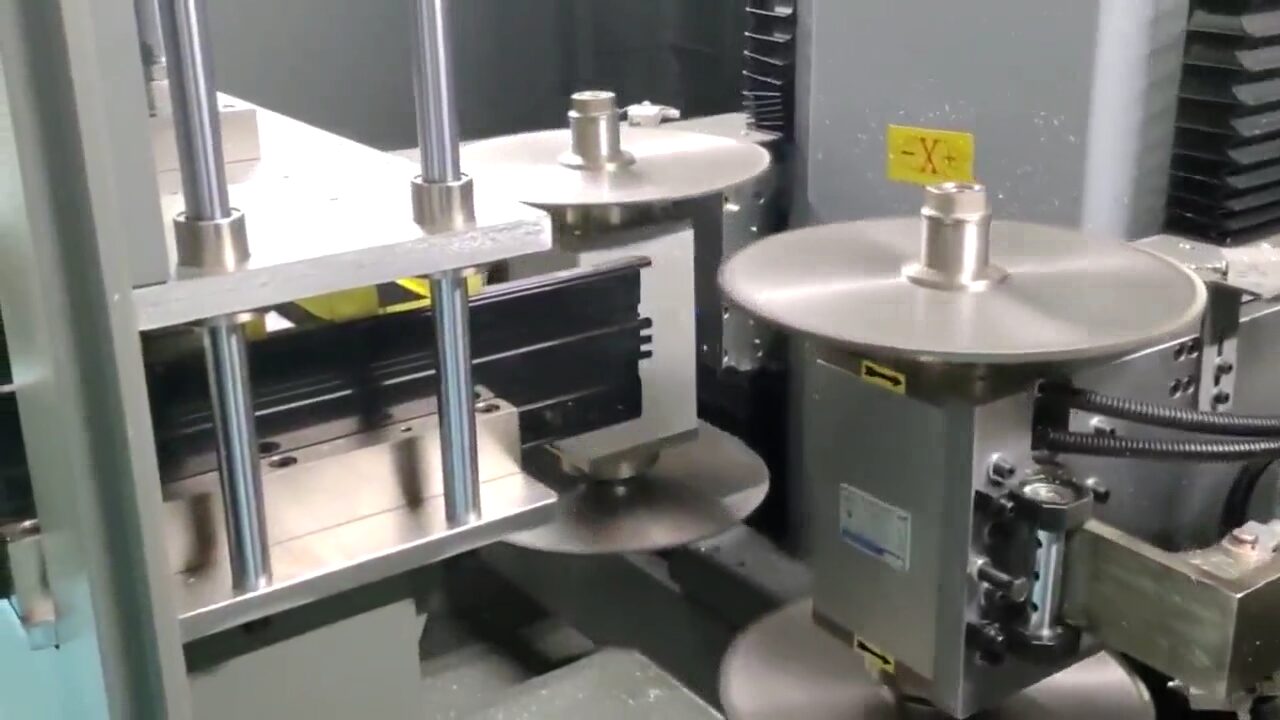
High-speed precision spindle motors are the driving force behind modern machining and manufacturing. Whether in metal cutting, woodworking, plastic processing, or stone engraving, the performance of a spindle motor directly impacts the efficiency, accuracy, and quality of the final product. But what makes a spindle motor deliver exceptional cutting performance? How do speed, torque, and cooling methods influence the results?
In this article, we will take an in-depth look at the cutting effects of high-speed precision spindle motors, exploring the key factors that determine their performance and how they optimize machining processes across different industries.
Key Factors Influencing the Cutting Effect of High-Speed Spindle Motors
Several crucial aspects affect the cutting performance of a spindle motor. Understanding these factors will help operators and manufacturers make the most of their spindle motors.
1. Rotational Speed and Cutting Efficiency
One of the most defining features of a high-speed precision spindle motor is its rotational speed, measured in revolutions per minute (RPM). The speed at which the spindle rotates plays a key role in determining:
- Material Removal Rate (MRR): Higher RPM allows for faster cutting, reducing processing time and increasing output.
- Surface Finish: A properly calibrated spindle speed can achieve ultra-smooth finishes, minimizing the need for additional polishing or sanding.
- Tool Longevity: Running at an optimal speed prevents excessive wear and tear on cutting tools, extending their lifespan.
For instance, in CNC metal milling, a 12,000 RPM spindle motor can deliver fine, precise cuts in aluminum and brass, whereas a lower-speed motor may struggle with clean edge definition.
2. Torque and Cutting Stability
Torque is the rotational force of the spindle, and it plays a significant role in determining how well the spindle handles different materials. A high-speed spindle with insufficient torque may struggle with heavy-duty cutting, leading to poor performance.
- High-Torque Spindles: Best suited for cutting dense materials like stainless steel, stone, and hard plastics.
- Low-Torque Spindles: Ideal for fine engraving, PCB drilling, and other delicate operations.
When choosing a spindle motor, balancing speed and torque is critical to achieving both precision and power in cutting applications.
3. Cooling Methods and Thermal Stability
High-speed spindle motors generate significant heat due to friction and prolonged operation. Without proper cooling, overheating can lead to:
- Reduced cutting accuracy
- Premature bearing wear
- Shortened motor lifespan
The two primary cooling methods used in spindle motors are:
Air-Cooled High-Speed Spindle Motors
✅ Simpler structure, easy to maintain
✅ Suitable for moderate workloads
✅ Best for woodworking, light milling, and engraving
Water-Cooled High-Speed Spindle Motors
✅ Superior heat dissipation for continuous operation
✅ Ideal for high-speed, high-precision cutting
✅ Preferred for metal, glass, and stone processing
A proper cooling system ensures the spindle motor maintains consistent cutting performance without compromising durability.
High-Speed Spindle Motors Cutting Effects in Different Industries
The cutting effect of a high-speed precision spindle motor varies across industries, each requiring unique optimizations for best results.
1. CNC Metalworking & Engraving
Spindle motors used in metal processing must deliver high torque and stability to handle hard materials such as aluminum, brass, and stainless steel. Common applications include:
✅ Milling: High-speed rotation ensures smooth, precise cutting edges.
✅ Engraving: Fine engraving on metal parts requires ultra-precise speed control.
✅ Drilling: Consistent torque prevents tool breakage when drilling small holes.
2. Woodworking & Furniture Manufacturing
In woodworking, a high-speed spindle motor ensures clean cuts without burning the material. Some key applications include:
✅ Panel Cutting: Efficiently slices through MDF, plywood, and hardwood.
✅ CNC Carving: ATC (Automatic Tool Change) spindles enable rapid switching between different router bits for detailed engravings.
✅ Edge Finishing: High-speed rotation provides smooth, splinter-free edges.
3. Plastic & Acrylic Processing
Cutting plastic materials like PVC, acrylic, and polycarbonate requires a stable, high-speed spindle to avoid melting or deformation.
✅ Acrylic Cutting: Delivers polished, crystal-clear edges.
✅ Plastic Engraving: Ensures sharp and accurate detailing.
4. Stone & Glass Cutting
Stone and glass require diamond tools paired with high-speed spindle motors for effective cutting.
✅ Granite & Marble Cutting: High-torque spindles ensure precision in natural stone processing.
✅ Glass Engraving: Prevents chipping and cracking with controlled speed and feed rates.
How to Optimize the Cutting Effect of a Spindle Motor
To achieve the best cutting results, proper optimization of the spindle motor is essential. Here are some expert recommendations:
🔹 Match RPM to the Material: Different materials require different speeds—adjust accordingly for the best surface finish.
🔹 Use High-Quality Cutting Tools: Dull or low-quality tools reduce efficiency and damage workpieces.
🔹 Ensure Proper Lubrication & Cooling: Helps maintain performance in high-speed operations.
🔹 Perform Regular Maintenance: Cleaning and lubricating spindle bearings prolongs motor life.
High-speed precision spindle motors are essential for achieving outstanding cutting effects in multiple industries. By optimizing speed, torque, cooling, and tooling, manufacturers can significantly enhance production efficiency, product quality, and tool longevity.
Investing in the right spindle motor and fine-tuning its parameters will ensure stable performance, minimal waste, and a competitive edge in the machining industry. Whether for metalworking, woodworking, plastic cutting, or stone engraving, a high-quality spindle motor is the key to unlocking superior cutting precision.